
680 KG / 1,500 LB
PAYLOAD

880 KM / 540 MI
range

220 KPH / 136 MPH
SPEED

UP TO 4 HOURS
OPERATING TIME

WEATHER
RESISTANT

REDUCED
HOURLY COSTS
our vision
The aviation industry is changing dramatically. Thanks to its rapid development, we are observing new VTOL solutions gradually entering a comparatively new Unmanned Aerial Systems market. These include tiltrotors, air taxis and cargo drones.
It is our mission and passion to create solid, cutting-edge products. These are an affordable civil tiltrotor for passenger and cargo transportation serving as an alternative to light aviation and other air taxi projects, and a cargo drone capable of transporting heavy payload, including to the regions with undeveloped infrastructure, and performing a wide variety of tasks in the air as a helicopter but with less noise, less hourly cost and at zero risk to the crew.
 READ MORE
At the current stage, we are focusing on the Drone project as it is less complex and demanding in terms of design, certification and development cost.
By bringing this product to the market, we will contribute to solving the most pressing and complex issues in the field of logistics, human health and safety:
- the last mile problem,
- provision of hard-to-reach regions,
- urgent delivery of medicines and vaccines,
- delivery of humanitarian cargo,
- work in the area of natural disasters,
- crew safety during missions,
- work in harsh weather conditions and low visibility.
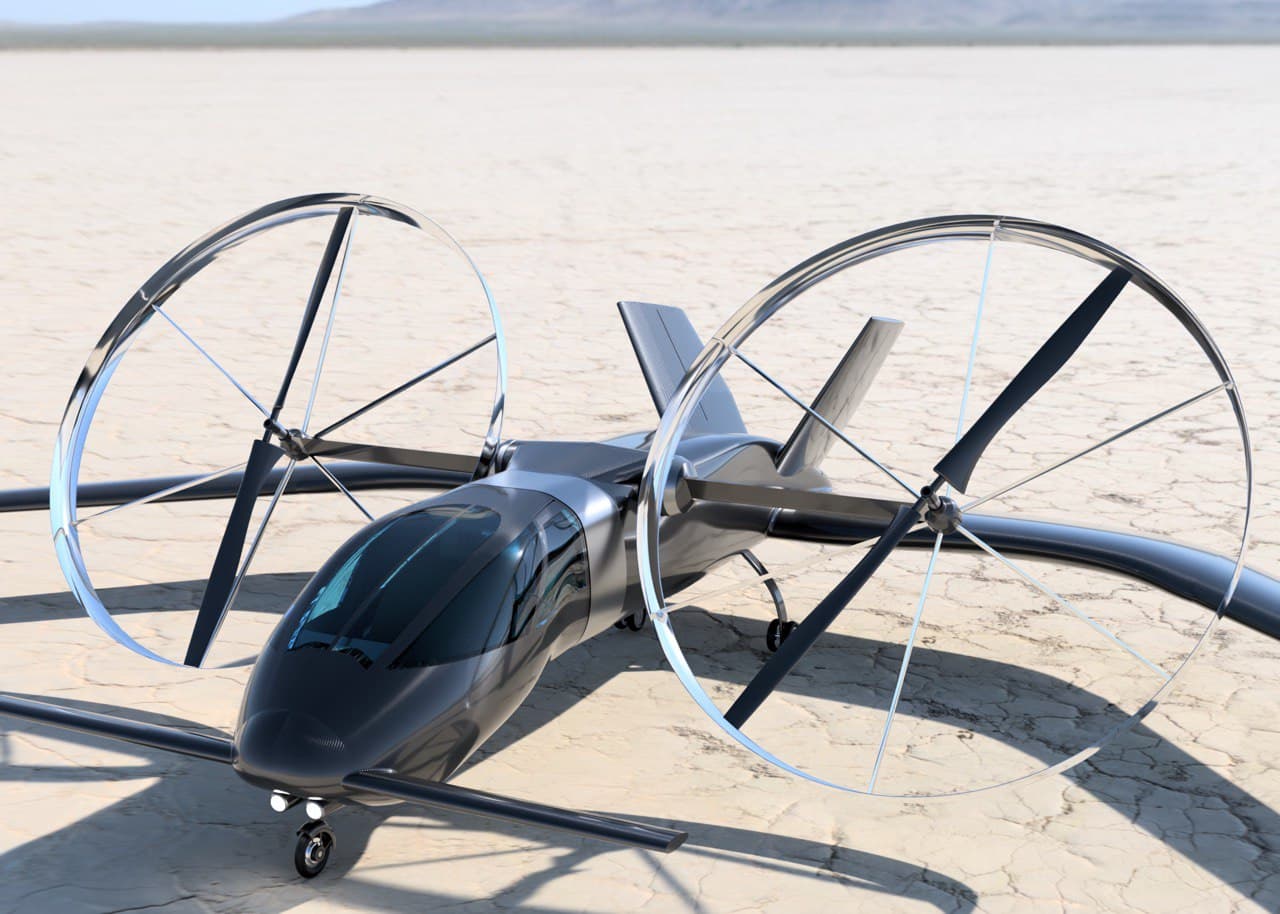
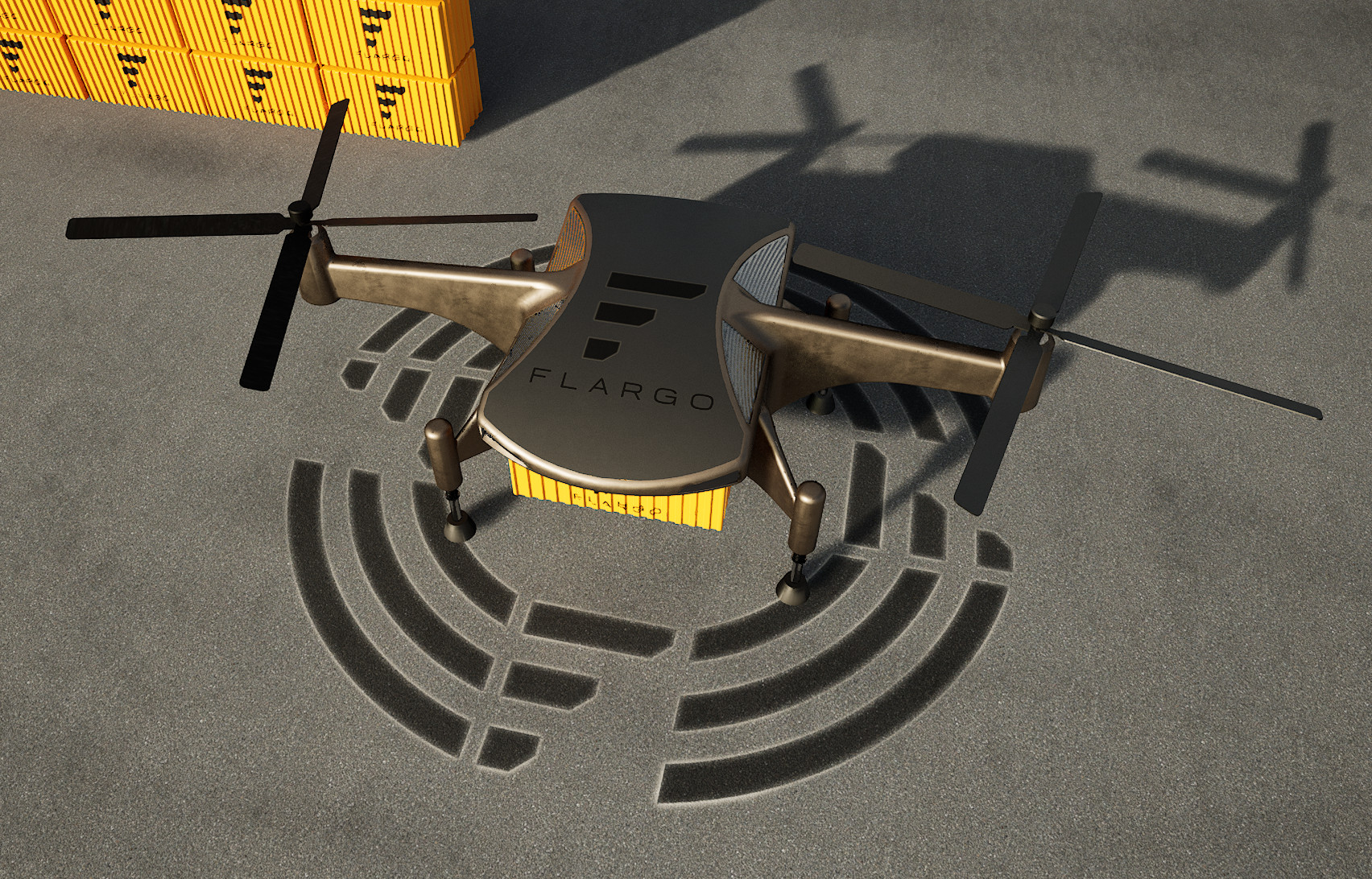
VTOL SOLUTIONS
Delivery by air is the most expeditious. But airplanes are not always an optimal solution due to possible lack of a runway or complexity of a logistics chain. Currently, helicopters are considered to be the most efficient VTOL solution. However there is a great market demand for other VTOL alternatives.
 READ MORE
In order to perform profound research and work on the VTOL technology with the limited resources we had, we created a test bench. It was used to carry out commissioning and intermediate tests. Within the first R&D stage we completed the following scope of work: development of a pylon and engine control system, installation and configuration of a thrust measurement system, development of a gearbox with an integrated swashplate, etc. We also calculated the blade parameters of the tiltrotor demonstrator in vertical flight modes and balanced the blades. Preliminary tests showed operability of the equipment.
Within the following part of the R&D process necessary information on the thrust vector control was collected, the pylon control system was programmed, and the code for microcontrollers was developed. Our data scientists managed to describe and justify the mathematical models and we finalized the pylon and swashplate control system. As a result, the test bench was controlled through the software environment. We performed calibration of the test bench, tested three different types of blades and various transmissions, added feedback to the linear drives of the swashplate.
In order not to embark on a too costly path of research, we decided to create a dynamic environment instead - we plan to expand the functionality of the current test bench and modify it into a mobile laboratory on wheels. Placing it on a pendulous stabilized platform should prevent turbulence caused by the truck. With the new option, we will be able to conduct various tests of the solutions we are working on.
technology
We have developed and patented a number of technological solutions based on the use of a swashplate. These include an adaptive transmission that is not subject to vibrations and allows us to eliminate most of the control-related issues. The mathematical modeling and AI-based controlling of two thrust vectors helped us maximize the controllability of the vehicles.
 READ MORE
We started R&D 5 years ago to challenge our ideas of creating a civil tiltrotor based on a modular VTOL platform concept. In the first place, we created a unique test bench and its 3 modifications to check our hypothesis and calculations. The concept proved to be viable, with 200+ hours of data collected on the bench.
Great efforts have been put into development of AI-based stabilization system which is one of the most valuable achievements of our team. Math models were matched with the neural network to result in the system that prevents emergency situations in case of any failures. The system autonomously finds complex solutions to control the vehicle.
As we firstly focused on the tiltrotor project, we managed to study transitional mode processes and thrust characteristics. We investigated the rotary node and control specifics. Modernization of the swashplate helped us develop a 360-degree thrust vector control system. The achieved thrust was 5 kg per 1 horsepower with small dimensions of the vehicle. The swashplate also solves the issues related to vibrations and allows the system operation at 2400 rpm.
Finally, we assembled a full-size demonstrator of a heavy lift drone that shows brilliant characteristics. The maximum take-off weight is 1070 kg with the dry weight of the vehicle being 380 kg.
We are working now on improving the mathematical model and testing the autopilot.
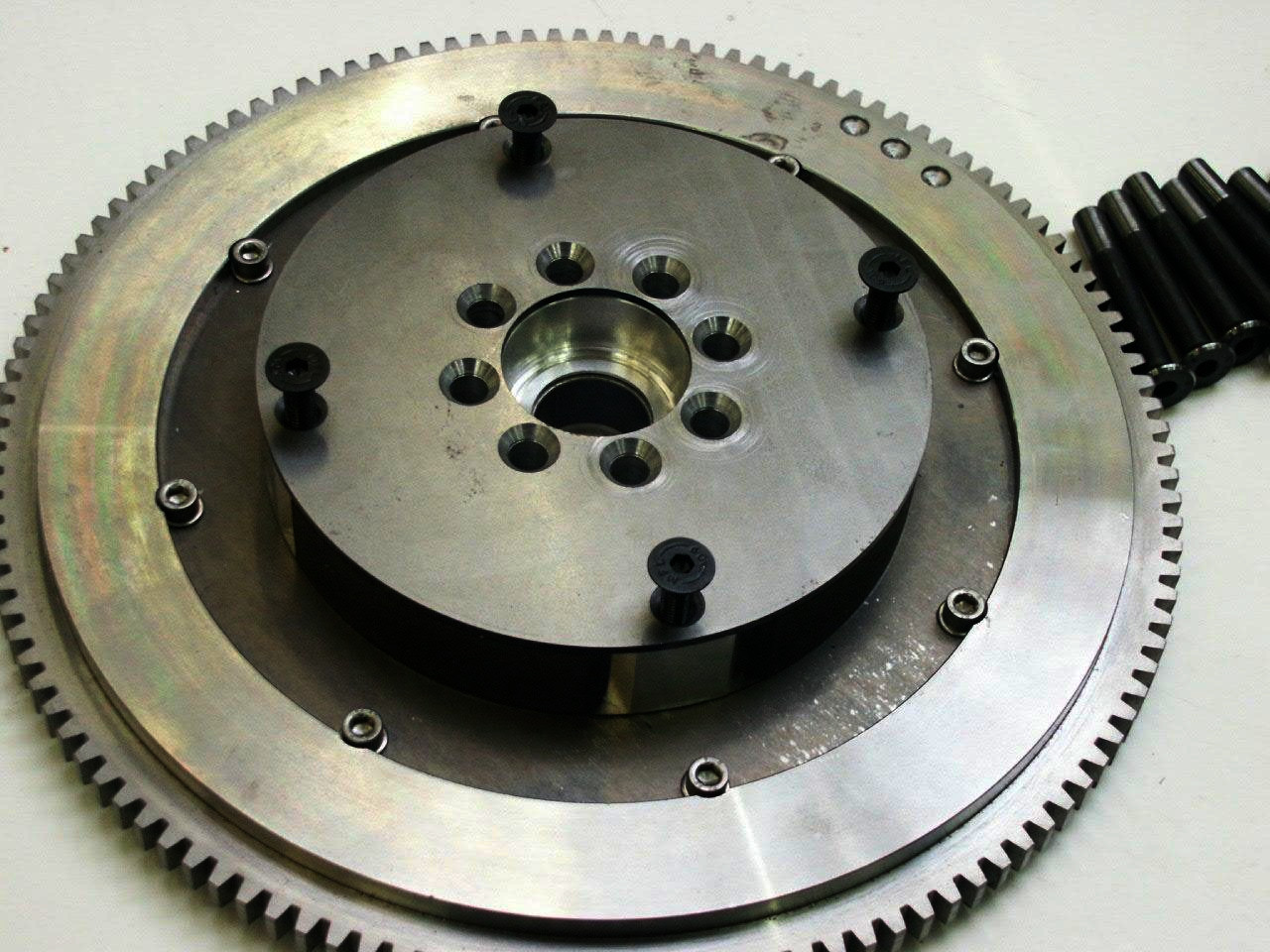
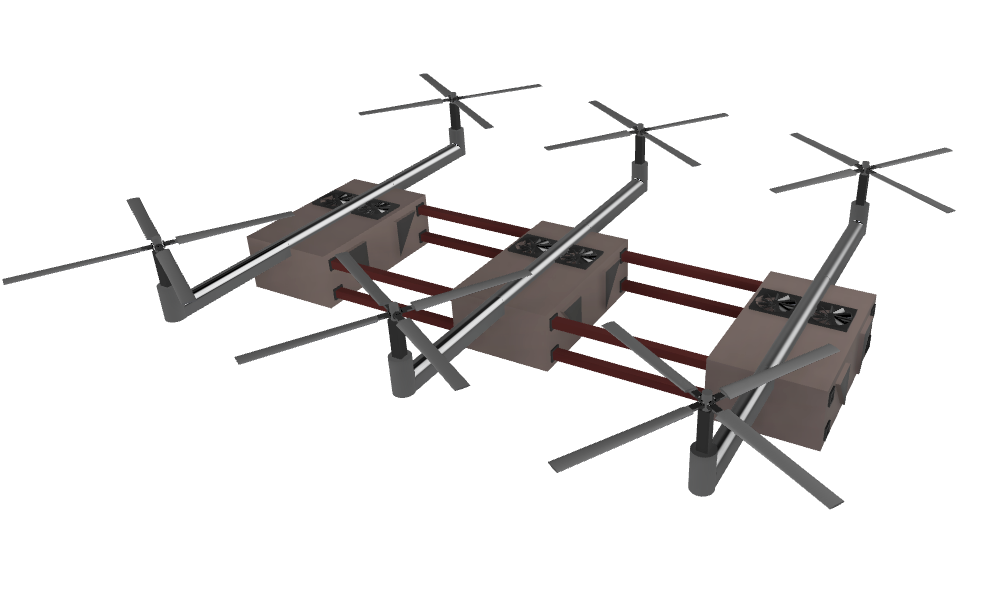
modular system
The modular platform can be modified as required to modernize the solution and to create new VTOL products. This concept allows to use the advantages of both longitudinal and transverse control concepts. By adding new modules, we can significantly increase the drone payload to meet high-level requirements. One module is capable of adding up to 680 kg of useful payload. It is possible to combine up to 4 modules.
READ MORE
The designed swashplate can be modernized for operating with two and four blades by adding or removing functional parts. Both options are efficient and are selected depending on the requirements for payload and the blades type.
We also can use various types of engine to operate with the current transmission. These are, for example, a turboshaft engine which is considered to be the most efficient in present, or alternatively a hybrid engine.
In addition, we can combine several platforms to get a 2-, 4-, 6- and even 8-rotor drone. This increases productivity in terms of lifting force.
POWER SOURCE
We are currently using an aviation piston engine organized as a central propulsion system. This concept works best for a vertical take-off which requires high energy consumption. Our concept also allows to use a turboshaft engine without need for complex modernization.
Hybrid technology can also be used as a propulsion system.
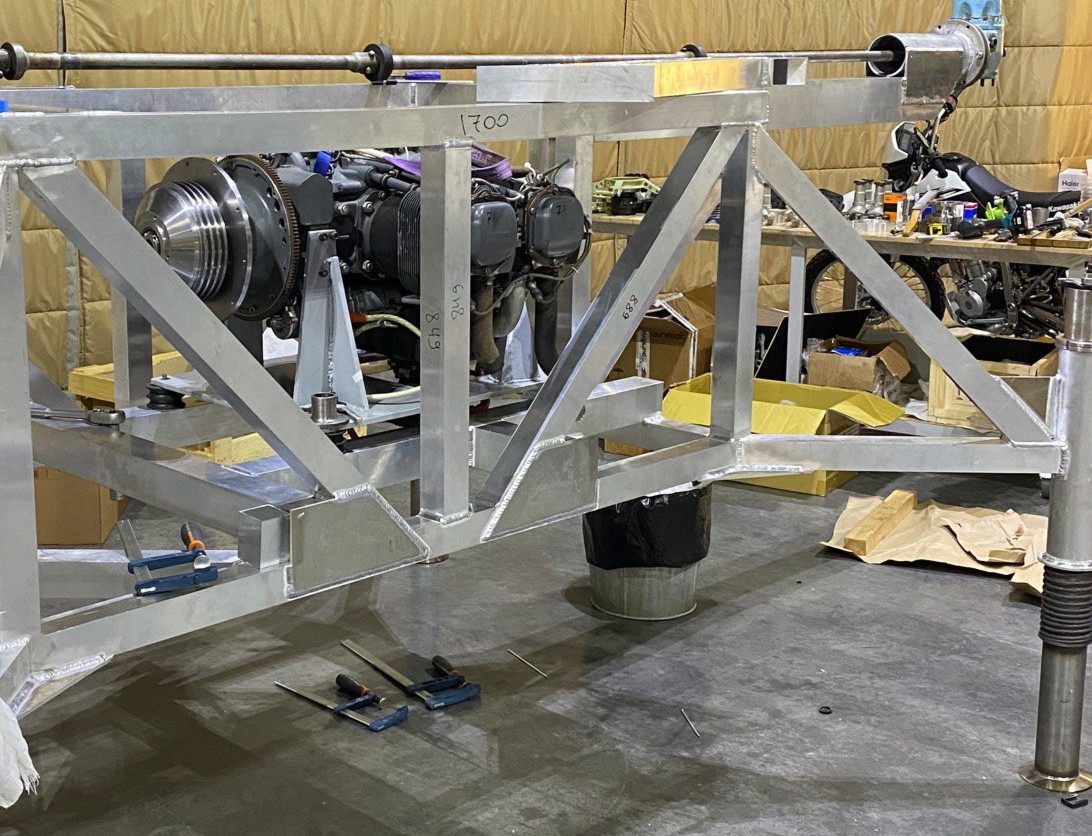
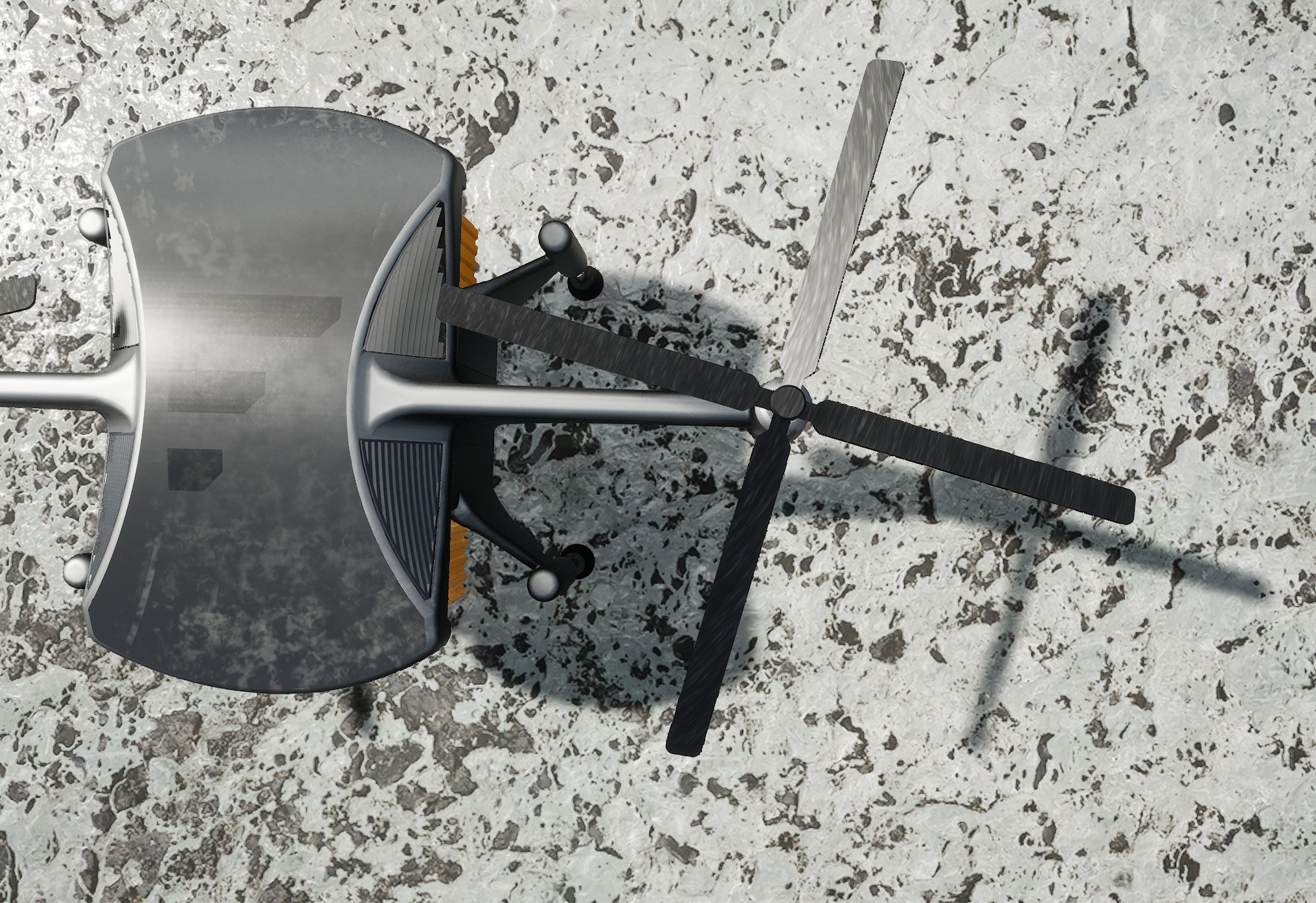
additional advantages
- work in icing conditions
- possibility of long-term operation up to 4 hours
- low cost of training a drone operator
- low flight hour operating cost
- autorotation
- reduced noise
- quick launch time
 READ MORE
The majority of modern VTOL projects in aviation are based on electric batteries which are used as the main source of energy. This approach is very practical at short distance but it has a significant disadvantage when it comes to high-altitude- or long-distance flights, including those in harsh weather conditions. We initially worked on the concept of a vehicle capable of functioning at subzero temperatures. The use of an internal combustion engine gives us excess to heat ,which we can be redistributed to heat critical components of the drone and prevent icing.
Due to the increased load capacity, the ratio of 5.1 kg of thrust to 1kW has been achieved at the moment. Estimated potential is 7.2:1. It gives us the possibility to stock up enough fuel and spend more time in the air if compared to other VTOL solutions.
When it comes to the cost of the solutions, it is worth noting that the unmanned technology we are applying makes it possible to significantly reduce the cost of training maintenance personnel. Automation takes over all key aspects of maintaining life of the drone, as well as low-level control of the device itself. Even a manual mode of the operator’s direct control is carried out through the Fly-by-Wire (FBW) interface. The key and critical operations, such as stabilization and action in the event of engine failure, are taken over by the electronics, thereby minimizing the human factor. In total, these solutions can significantly reduce the cost of training a remote control operator, compared to the cost of training a helicopter or airplane pilot.
In addition, the concept and technology we have developed allows to significantly reduce the flight hour operating cost.
Another practical and useful feature is the drone’s capability to take-off and start operation after only 5 minutes in an accelerated mode. Immediately after the drone can take off to perform a task.
professional team
We are proud to have in our team professionals who have passion for aviation and solid background in engineering, aviation and helicopter construction, data science, programming, 3D modeling, marketing and logistics.
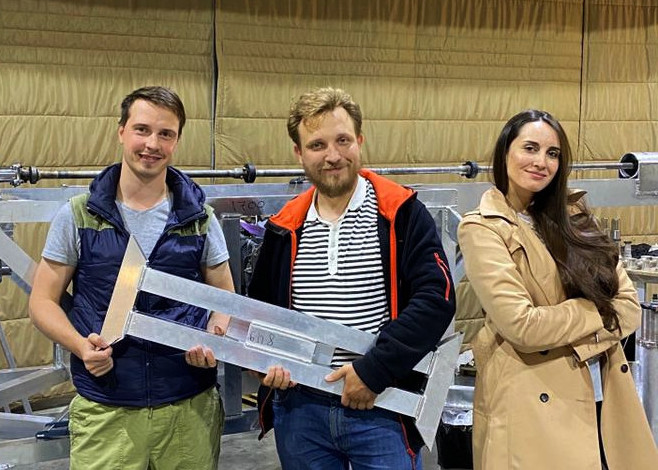