Obtaining maximum thrust with minimum losses
Autonomous vehicles have firmly entered our life, new industries and business segments are emerging. Drones serve warehouses and logistics hubs, monitor objects and even deliver pizza. One of the most sought-after solutions is VTOL drones, which require minimal infrastructure to operate.
When analyzing autonomous solutions, it can be noted that most of them are driven by an electrical engine. But eVTOL cannot fully cover all the needs of market operators. Main limiting factors are:
- energy costs in hovering modes,
- use of fixed pitch propellers,
- excessive duplication of motors and electrical circuits,
- small amount of energy capacity.
Our team is developing a drone with a thrust comparable to that of a helicopter. Something that can become a real alternative to helicopters in terms of payload, range and operating time.
There are several main tasks:
- achieve maximum thrust with minimum energy losses,
- gain speed comparable to helicopters or higher,
- significantly reduce noise level compared to helicopters.
As the main aerodynamic scheme, we use a twin-rotor configuration as the most promising and stable. This gives us the opportunity to minimize energy losses for the stabilization of the vehicle. To control the thrust vector, we use a swashplate, which we have developed specifically for our drone, taking into account all the necessary requirements.
To reduce noise, we had a very limited set of options, and in the end, we decided to reduce the length of the blades. To maintain lift, we increased the blade rotation speed and the number of blades. At the same time, in order to reduce weight and be more compact, as well as to obtain some additional benefits, we placed the blades in two levels. The addition of a second tier of blades further increased the stabilization of the drone, but we experienced a loss in thrust initially. This was due to the lower level of the blades getting into the air turbulence from the upper level.
We performed primary calculations for two blades. Subsequent tests on the test bench confirmed the calculated thrust values.
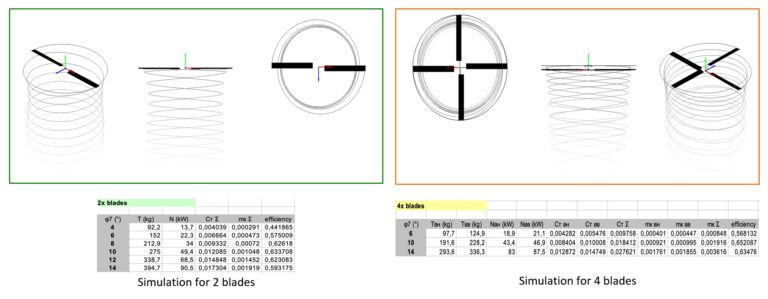
For the initial calculation, we used 80% of the available power of the engine and various angles of attack.
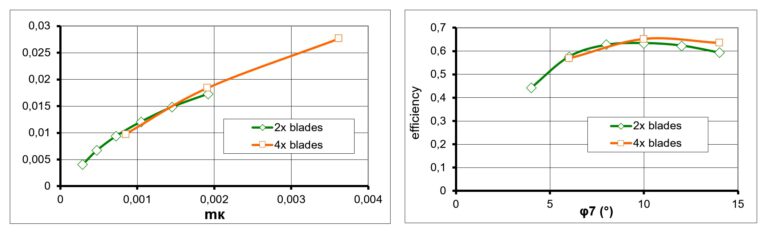
The tests carried out showed that after reaching a certain speed, there is a drop in thrust by 12% below the calculated ones. Since we originally designed our swashplate with the ability to change the X-shape of the propeller, this allowed us to change the angle between the upper and lower levels of the blades.
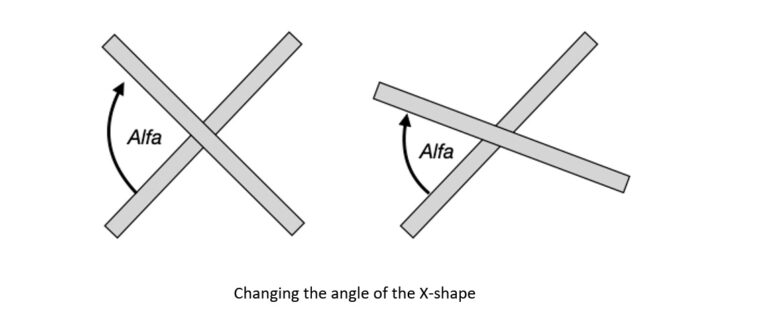
Changing the angle between the blades made it possible to shift the dips in thrust associated with the turbulence of the upper layer to a different speed.
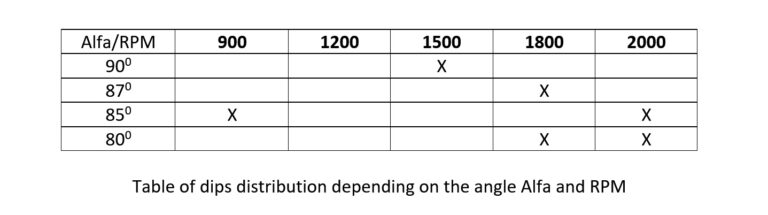
Based on the results of research work, we have made changes to the design of the swashplate to adaptively change the angle Alfa from the rotation speed. As a result of the tests, the occurrence of drawdown in traction was reduced to 6 percent.
As a result of the experiments, we managed to obtain a uniform increase in power without the occurrence of parasitic vibrations. The total thrust per pylon approached the theoretically calculated one without taking into account turbulence from the upper level of the propeller.
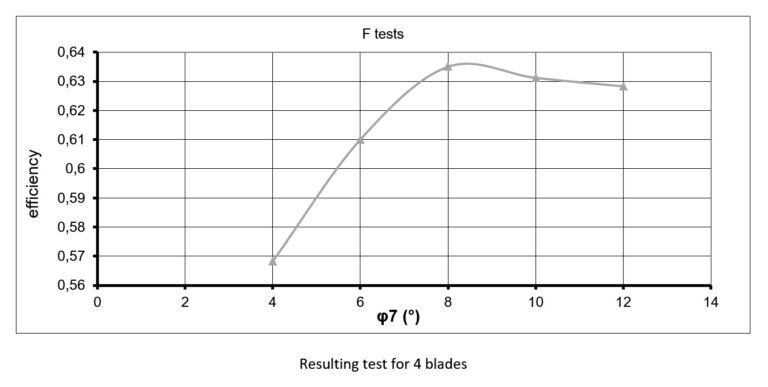
Thanks to the developments made, our team was able to achieve maximum thrust with existing power.
And the main result achieved is that the changes made in the course of work to the plate and the mechanization of the swashplate made it possible to significantly increase the efficiency of the propeller.
The next improvement step is to switch to a different blade profile.
AUTOROTATION
Flargo innovations
SWASHPLATE AND TRANSMISSION, DESIGNED AS A SINGLE KEY UNIT
We have designed and created a transmission based on a single synchronizing shaft, a centrifugal clutch and an upgraded swashplate. To control the thrust vector, we use a mathematical model developed by us.
This made it possible to create a united system with a number of key advantages over analogues.
The modernized swashplate contains a combination of unique features that are not found in any solution being developed or an existing one, known to us:
a) The best lifting performance for 4 propellers with a diameter of up to 340 cm, with the ability to work at speeds up to 2000 rpm.
This solution gives significant advantages over constant pitch propellers on electric motors, as by using the helicopter control concept, we can change the thrust vector without changing the speed of blades rotation. At the same time, controllability remains at the level of helicopters.
During the tests, a thrust-to-power ratio of 5.5 kg per 1 hp was obtained. This corresponds to the characteristics of modern helicopters, but is achieved with less fuel consumption.
b) The developed concept allows us to get rid of parasitic vibrations inherent in helicopters with a single-rotor scheme which complicate the control process and require the use of expensive technical solutions to eliminate them.
c) Due to the use of a centrifugal clutch working in conjunction with a single rotating shaft, the possibility of rapid start is achieved. Despite the fact that it is recommended to warm up the engine under standard conditions, it is possible to enter takeoff mode without it, if necessary. The whole process will take about a minute.
d) The application of the concept based on the swashplate and a single synchronizing shaft provides the possibility of using the autorotation mode.
This gives us at least two advantages over projects using a parachute rescue system:
1) it is not necessary to sacrifice the payload,
2) autorotation works at low altitudes, while a ballistic parachute is ineffective below 60 meters.
e) The transmission we have created allows the use of various types of powerplants, including hybrid engines potentially, without making significant changes to the design. Nevertheless, in present we can get the optimal operating mode and savings by using internal combustion engines and turboshaft engines.
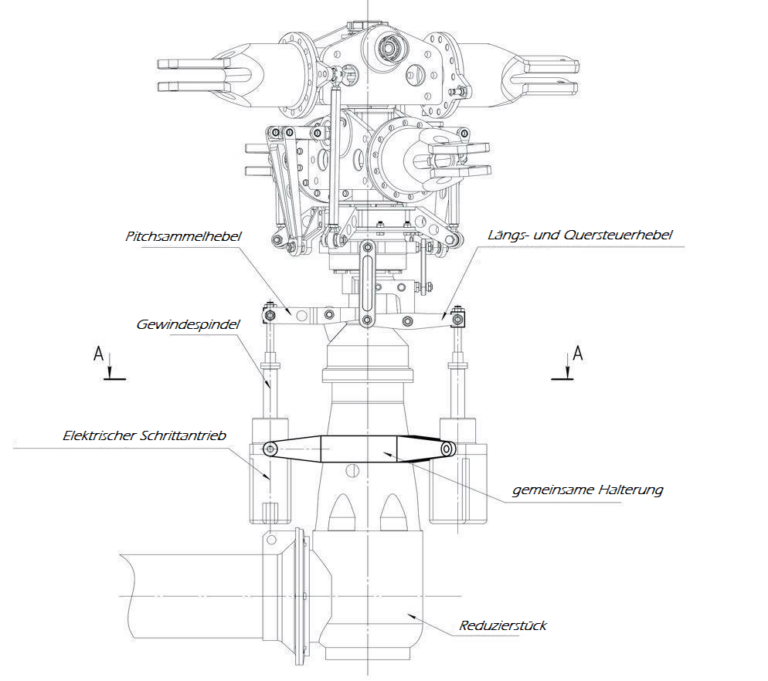
INTELLIGENT CONTROL SYSTEM BASED ON MATHEMATICAL MODEL
We initially focused on using the concept of a rotary rotor. Therefore, the mathematical model being developed and used in autopilot is designed for the concept of a rotary pylon. In case of using a fixed node, this provides capabilities comparable to those of twin-rotor helicopters, such as the Chinook or the Soviet prototype V-12 (Mi-12).
The change in the thrust vector is achieved with the help of the automatic swashplate, which results in significant advantages in speed and load capacity, compared to other cargo drone projects. If analyzing a large number of existing projects, changing in the rotation speed of fixed-pitch propellers is used to create a roll and obtain the necessary pitch angle. Despite the simplicity of such a solution, its efficiency in terms of energy use and controllability is very low. It is also worth noting that many of these solutions are not scalable and cannot be used if the device weight or cargo weight being lifted is increased.
The mathematical model we are developing allows to operate with the thrust vector of two, four, six or even eight propellers. This, in its turn, lays the foundation of a modular concept, which potentially makes it possible to put together several modules of the lifting platform (up to four) and obtain various thrust characteristics.
AUTOROTATION
Autorotation
The key safety benefit of our solution is the unmanned technology itself. Which means zero risk to the crew.
But there is another important safety feature – the autorotation system.
A sudden loss of power / thrust is the possibility that should be always taken into account.
If the engine fails, the freewheeling unit automatically disengages it from the main rotor system allowing the rotors to rotate freely.
In this situation the blades are driven solely by the upward flow of air through the rotors (as opposed to a normal powered flight, when air is drawn into the main rotor system from above and exhausted downward).
During the maneuver the blades are producing sufficient lift and thrust by a combination of their angle of attack and velocity.
At a suitable height the so-called flare stage takes place. You can see it on the figure below (drone position no. 3 - in the middle): airspeed is reduced for a run-on landing using a decelerative, nose-up flare attitude. The flare has the benefit both of reducing forward speed and increasing RRPM (rotor revolutions per minute), necessary to cushion the touchdown. The additional lift created during the flare reduces the rate of descent.
When flying a helicopter, it is the pilot who makes decisions. In the Drone, electronics is responsible for everything based on real-time data analysis.
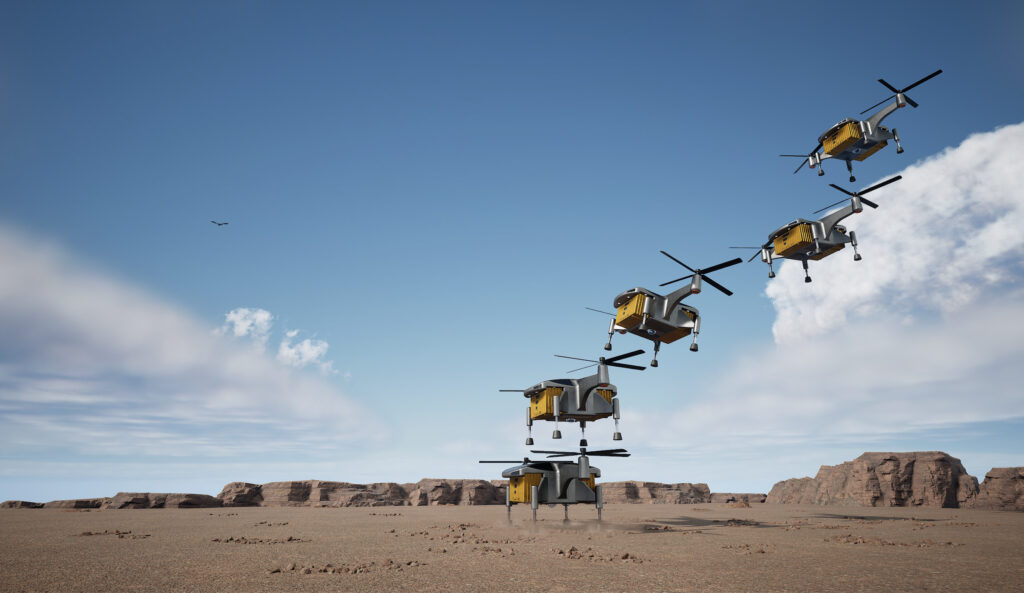